Расчет режимов фрезерования. Выбор рациональных режимов фрезерования. Виды инструментов для художественного фрезерования
ЭЛЕМЕНТАРНЫЕ ПОНЯТИЯ О ТЕОРИИ РЕЗАНИЯ
§ 10. ЭЛЕМЕНТЫ РЕЗАНИЯ ПРИ ФРЕЗЕРОВАНИИ
В процессе фрезерования зубья фрезы при ее вращении последовательно один за другим врезаются в надвигающуюся заготовку и снимают стружку, осуществляя резание.
Элементами резания при фрезеровании являются ширина фрезерования, глубина фрезерования, скорость резания и подача.
Режущие инструменты имеют различные размеры, материалы и типы геометрии. Как правило, более эффективно использовать комбинацию различных траекторий и инструментов для достижения детальной модели, а не предполагать, что единственный инструмент с меньшим переходом - единственный способ. Часто более крупный инструмент может достичь лучших результатов.
В концевом фрезеровании режущий инструмент обычно вращается по оси, вертикальной по отношению к заготовке. Режущие зубы расположены как на торце режущего инструмента, так и на периферии корпуса резака. Концевая мельница с шариком, также известная как сферическая концевая мельница или шаровая концевая мельница, имеет полусферу на конце инструмента. Торцевые фрезы используются на заготовках со сложными поверхностями.
Ширина и глубина фрезерования
Шириной фрезерования называют ширину обрабатываемой поверхности в миллиметрах (рис. 52). Ширина фрезерования обозначается через В.
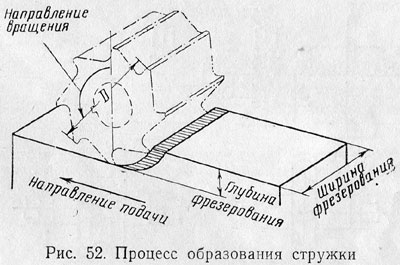
Глубиной резания при фрезеровании, или глубиной фрезерования
, или часто глубиной срезаемого слоя, называют толщину (в миллиметрах) слоя металла, снимаемого с поверхности заготовки фрезой за один проход, как это показано на рис. 52. Глубина фрезерования обозначается через t. Глубина фрезерования измеряется как расстояние между обрабатываемой и обработанной поверхностями.
Весь слой металла, который необходимо удалить при фрезеровании, называется, как указывалось выше, припуском на обработку. Глубина фрезерования зависит от припуска на обработку и мощности станка. Если припуск велик, обработку производят в несколько переходов. При этом последний переход производят с небольшой глубиной резания для получения более чистой поверхности обработки. Такой переход называют чистовым фрезерованием в отличие от чернового, или предварительного фрезерования, которое производят с большей глубиной
фрезерования. При небольшом припуске на обработку фрезерование производят обычно с одного прохода.
Выбор плоской торцовой фрезы против шаровой торцовой фрезы определит характеристики меток на вашей модели. Большинство рабочих мест выиграют от стратегического использования нескольких инструментов размера и формы для фрезерования различных функций. Имеются вырезанные, обрезанные, обрезные концевые мельницы с различным количеством канавок. Концевые фрезы предназначены для разрезания по горизонтали.
Виды инструментов для художественного фрезерования
Обрезка, обрезание и сжатие определяют способ выталкивания стружки и гладкость поверхности. С помощью концевой фрезы чипы будут выбрасываться вверх, а нижняя часть материала будет гладкой. Срезанная концевая мельница имеет обратную сторону, опуская чипы вниз, а верхняя часть материала гладкая. Концевая мельница сжатия создает гладкую поверхность сверху и снизу, которая идеально подходит для предварительно ламинированных лесов.
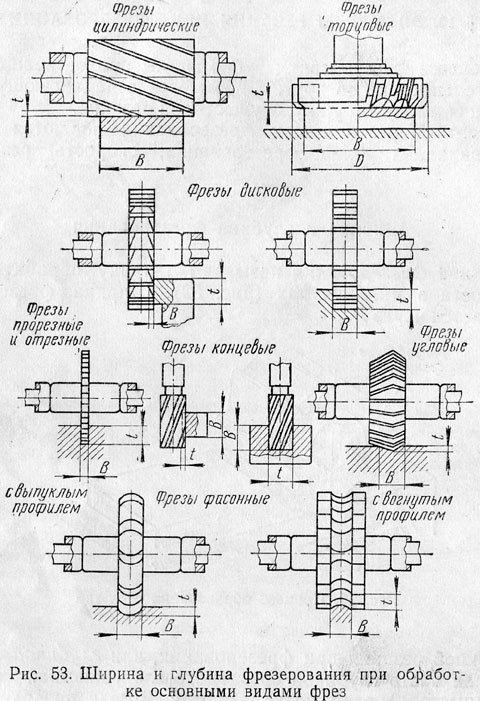
На рис. 53 показана ширина В и глубина фрезерования t при обработке основными видами фрез.
Скорость резания
Главным движением при фрезеровании является вращение фрезы. В процессе фрезерования фреза вращается с определенным числом оборотов, которое устанавливается при настройке станка; однако для характеристики вращения фрезы принимают не число ее оборотов, а так называемую скорость резания.
Скоростью резания
при фрезеровании называют путь, который проходят в одну минуту наиболее отдаленные от оси точки режущей кромки зуба фрезы. Скорость резания обозначается через υ.
Обозначим диаметр фрезы через D
и предположим, что фреза делает один оборот в минуту. В этом случае режущая кромка зуба фрезы пройдет в минуту путь, равный длине окружности диаметра D мм
, т. е. πD
миллиметров. В действительности фреза делает больше одного оборота в минуту. Предположим, что фреза делает n
оборотов в минуту, тогда режущая кромка каждого зуба фрезы пройдет в одну минуту путь, равный πDn мм
. Следовательно, скорость резания при фрезеровании равна πDn мм/мин
.
Обычно скорость резания при фрезеровании выражают в метрах в минуту, для чего необходимо полученное выражение скорости в мм/мин
разделить на 1000. Тогда формула скорости резания при фрезеровании примет вид:
Концевые мельницы бывают разных форм. Наиболее распространенными являются плоские торцевые фрезы и шаровые мельницы. Плоские торцевые фрезы разрезают плоские участки без гребешков. Тем не менее, они оставляют террасообразный гребешок на не-плоских поверхностях. На торцевых мельницах с шариками останутся меньшие морские гребешки с одинаковым значением перелома на наклонных поверхностях, но они также оставят морские гребешки на плоских участках.
Модели могут быть оснащены комбинацией плоских и шаровых мельниц. Если для всех поверхностей будет использоваться только один инструмент, геометрия шарового конца даст более последовательное общее ощущение и гладкий результат. Плоские торцевые фрезы могут быть центрированными и нецентральными режущими инструментами: Центробежные торцовые фрезерные станки необходимы для фрезерования. Нецентровые фрезерные станки используются только для бокового фрезерования.

Из формулы (1) следует, что чем больше диаметр D фрезы, тем больше скорость резания при данном числе оборотов, и чем больше число оборотов n шпинделя, тем больше скорость резания при данном диаметре фрезы.
Пример 1
. Фреза диаметром 100 мм делает 140 об/мин. Определить скорость резания.
В данном случае D
= 100 мм
; n
= 140 об/мин
. По формуле (1) имеем:
При выборе шаровой мельницы всегда выбирается самый большой размер. Для такого же усовершенствования более крупный инструмент оставит меньшие гребешки, что даст более плавный результат. Для обычно гладкой модели с некоторыми областями мелкой детали, большой инструмент должен использоваться для общей работы, а меньший инструмент должен использоваться только для очистки подробных областей.
Расчет скорости резания
Более крупные инструменты вырезаются более чисто, имеют больший зазор и остаются острыми дольше. Скорость режущей кромки на более крупном инструменте выше для той же скорости шпинделя. Значение пошагового определения будет определять, имеет ли модель гладкую поверхность или видны метки инструментов. Это также будет напрямую влиять на время резания. Модели с меньшей степенью защиты занимают больше времени.
На производстве часто приходится решать обратную задачу: по заданной скорости резания υ определить число оборотов фрезы n
или ее диаметр D
.
Для этой цели применяют формулы:
Пример 2
. Обработку предложено производить при скорости резания 33 м/мин
. Фреза имеет диаметр 100 мм
. Сколько оборотов надо дать фрезе?
В данном случае υ = 33 м/мин
; D
= 100 мм
.
По формуле (2а) имеем:
Налипание смол на фрезу
Длина области резания внутри инструмента определяет, насколько глубоко материал может быть разрезан за одну операцию - это называется максимальным уклоном. Это значение отступов будет использоваться только до максимума, когда материал, который режется, является мягким; для более твердых материалов часто требуется меньшее значение, устанавливая траектории инструмента для измельчения слоев материалов в отдельных проходах.
Хотя количество, направление и тип флейт, которые режущий инструмент имеет, могут широко варьироваться, инструменты, которые обычно используются, имеют две канавки и имеют разреженные спирали. Некоторые проекты могут извлечь выгоду из других типов геометрии флейты.
Пример 3.
Скорость резания составляет 33 м/мин
. Число оборотов фрезы составляет 105 об/мин
. Определить диаметр фрезы, которую надо применить для данной обработки.
В данном случае υ = 33 м/мин
; n
= 105 об/мин
.
По формуле (26) получаем:
Не всегда на станке можно установить число оборотов шпинделя в минуту, которое точно соответствует полученному по формуле (2а). Также не всегда удается подобрать фрезу точно того диаметра, (который получается по формуле (26). В этих случаях берут ближайшее меньшее число оборотов шпинделя в минуту из имеющихся на станке и фрезу с ближайшим меньшим диаметрам из имеющихся в кладовой.
Одиночная флейта. Позволяет использовать более крупные стружки в более мягких материалах. Двойная флейта - позволяет улучшить отделку деталей в более твердых материалах. Множественные флейты. Позволяет еще лучше закончить отделку в более твердых материалах.
По мере увеличения количества режущих кромок ваша скорость подачи должна увеличиваться, чтобы предотвратить сжигание и преждевременное смачивание инструмента. Больше канавок уменьшает нагрузку на стружку и улучшает чистоту поверхности, если скорость подачи остается неизменной. Наиболее распространенными номерами флейт для общих операций фрезерования являются два и четыре.
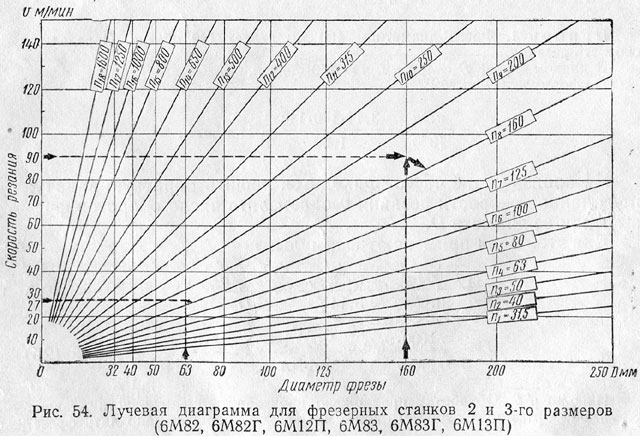
Для определения числа оборотов шпинделя при заданной скорости резания и выбранном диаметре фрезы можно пользоваться графиками. На графике рис. 54 указаны располагаемые числа оборотов шпинделя консольно-фрезерных станков второго и третьего размеров (6М82, 6М82Г и 6М12П, 6М83, 6М83Г и 6М13П), изображенные в виде лучей, вследствие чего такие графики называют лучевыми диаграммами
. На горизонтальной оси отложены диаметры фрез в мм
, а по вертикальной оси - скорости резания в м/мин
. Пользование графиком поясняется следующими примерами.
Пример 4
. Определить число оборотов шпинделя консольно-фрезерного станка 6М82Г при обработке стали цилиндрической фрезой из быстрорежущей стали диаметром 63 мм
, если задана скорость резания υ = 27 м/мин
.
По графику на рис. 54 от точки, соответствующей скорости резания 27 м/мин
, проводим горизонтальную линию до пересечения с вертикальной линией, проведенной от точки, соответствующей диаметру фрезы 63 мм
n
= 125 и n
= 160. Принимаем меньшее число оборотов n
= 125 об/мин
.
Пример 5
. Определить число оборотов шпинделя консольно-фрезерно-го станка 6М13П при обработке чугуна торцовой фрезой диаметром 160 мм
, оснащенной твердым сплавом, если задана скорость резания υ = 90 м/мин
.
По графику на рис. 54 от точки, соответствующей скорости резания 90 м/мин
, проводим горизонтальную линию до пересечения с вертикальной линией, проведенной от точки, соответствующей диаметру фрезы в 160 мм
. Искомое число оборотов шпинделя лежит между n
= 160 и n
= 200. Принимаем меньшее число оборотов n
= 160 об/мин
.
Такую лучевую диаграмму нетрудно вычертить самому для станка другой модели и размера.
Применение лучевой диаграммы упрощает подбор числа оборотов шпинделя станка и позволяет обходиться без применения формулы (2а).
Примеры применений с использованием торцевых мельниц. Материал: торцевые фрезы изготавливаются либо из сплавов кобальтовой стали, либо из карбида вольфрама в решетке кобальта. Последний вариант значительно сложнее, жестче и более устойчив. При использовании твердосплавных инструментов убедитесь, что ваш станок жесткий с твердым шпинделем, и что у держателей мало или нет биения. Из-за хрупкого характера карбида и скоростей, с которыми обычно работают твердосплавные инструменты, жесткость имеет решающее значение для предотвращения разрушения инструмента.
ВЫБОР РЕЖИМА РЕЗАНИЯ ПРИ ФРЕЗЕРОВАНИИ
§ 78. УСЛОВИЯ, ОПРЕДЕЛЯЮЩИЕ ВЫБОР РЕЖИМА РЕЗАНИЯ
Понятие о наивыгоднейшем режиме резания
Наивыгоднейшим следует считать такой режим резания при работе на фрезерном станке, при котором наиболее удачно сочетаются скорость резания, подача и глубина срезаемого слоя, обеспечивающие в данных конкретных условиях (т. е. с учетом
наилучшего использования режущих свойств инструмента, скоростных и мощностных возможностей станка) наибольшую производительность труда и наименьшую стоимость операции при соблюдении заданных технических условий в отношении точности и чистоты обработки.
Научно-исследовательским институтом труда Государственного комитета Совета Министров СССР по вопросам труда и заработной платы разработаны при участии крупнейших отечественных ученых с учетом практического применения в производственных условиях режимы резания при фрезеровании инструментами из быстрорежущей стали и твердых сплавов. Они могут служить в качестве исходных данных при назначении скоростей резания и минутных подач.
Эти нормативы имеются на каждом заводе и служат руководящим материалом для разработки технологического процесса и составления операционных карт, подобно приведенной на стр. 204-205. Однако приведенные в них скорости резания и минутные подачи не являются предельными и в ряде случаев могут перекрываться фрезеровщиками, если применять более производительные инструменты или работать на более мощных и жестких станках.
С другой стороны, молодые, т. е. начинающие и не имеющие достаточного опыта, фрезеровщики не всегда могут работать на предельных режимах резания, поэтому для них предусмотрены в «Справочнике молодого фрезеровщика» менее жесткие режимы резания, начиная с которых, необходимо, по мере повышения квалификации, переходить к более жестким.
Чтобы самому внедрять новые режимы, надо знать порядок и последовательность установления режимов фрезерования.
Покрытия: карбидные фрезы могут быть дополнительно покрыты керамикой, такой как нитрид титана, нитрид титана, нитрид нитрата титана и так далее. Другие типы инструментов, используемых в нашей фабрике. Этот документ основан в разных источниках. Мы окружены множеством металлических изделий в нашей повседневной жизни. Вы знаете, как производятся эти продукты?
Существует много способов обработки металлов, но наиболее часто используемый метод - резка. Здесь мы узнаем о режущих инструментах и процессах резания. Что мы имеем в виду, говоря режущие инструменты? Во-первых, давайте посмотрим на некоторые примеры режущих инструментов, которые есть в нашей повседневной жизни. Ножи и терки на кухне, ножницы и точилки для карандашей на столе, а также пила и плоскость в кладовой - все режущие инструменты.
Материал режущей части фрезы
Решающим фактором, определяющим уровень режима резания, является материал режущей части фрезы. Как упоминалось выше, применение фрез с пластинками из твердого сплава позволяет работать на больших скоростях резания и больших подачах по сравнению с фрезами из быстрорежущей стали; как увидим далее, твердосплавные фрезы дают возможность повышения производительности в два-три раза против быстрорежущих. Поэтому твердосплавные фрезы целесообразно применять почти на всех видах фрезерной обработки; препятствием к их применению может явиться недостаточная мощность оборудования или специфические свойства материала обрабатываемой заготовки.
Однако в ряде случаев применение для режущей части фрез углеродистых, легированных инструментальных и быстрорежущих сталей является рациональным, особенно когда чистота обработанной поверхности и точность полученной поверхности детали имеют большее значение, чем скорость выполнения работы.
Выбор режима резания при фрезеровании
Эти режущие инструменты имеют общее свойство, которое заключается в том, что все они меняют формы вещей, сокращая и создавая чипы. Как вы уже знаете, режущие инструменты - это инструменты, которые режут предметы для получения желаемой формы. Теперь давайте посмотрим на режущие инструменты, которые стальная сталь, основной материал в промышленном мире.
Давайте посмотрим на процесс производства карбида. Во-первых, смешайте карбид вольфрама с кобальтом, чтобы получить порошок, который можно классифицировать как сырье. Гранулированную смесь выливают в полость матрицы и прессуют. Это дает умеренную силу, подобную мелу.
Геометрические параметры режущей части
Не менее важным фактором, влияющим на выбор режимов резания, являются геометрические параметры режущей части фрезы (режущих углов, размеров и формы зуба), что часто называют геометрией фрезы
. Ранее, в § 7, рассмотрены значение и влияние каждого из элементов геометрии зуба фрезы в процессе резания; здесь же рассмотрим рекомендуемые геометрические параметры режущей части фрез из быстрорежущей стали Р18 и с пластинками твердого сплава.
В табл. 35 и 36 приведены рекомендуемые значения геометрических параметров цилиндрических, торцовых, дисковых, отрезных, концевых и фасонных фрез из быстрорежущей стали.
После спекания объем содержимого значительно сокращается. Кроме того, твердость цементированного карбида находится на уровне между алмазом и сапфиром, а вес примерно в два раза выше, чем у железа. Затем, как мы разрезаем этот твердый цементированный карбид?
На рисунке справа показано состояние режущей кромки во время обработки. Режущая кромка разрезает заготовку и производится чип. Цементированные карбидные марки, которые могут выдерживать эти высокие температуры, являются наиболее успешными. Карбид, сформированный в различные конфигурации, является самым популярным, и они называются индексируемыми вставками. Индексируемые вставки используются для различных форм держателей и выбираются в соответствии с формой заготовки и режимом резания.
Таблица 35
Геометрические параметры режущей части фрез из быстрорежущей стали Р18
I. Передние углы
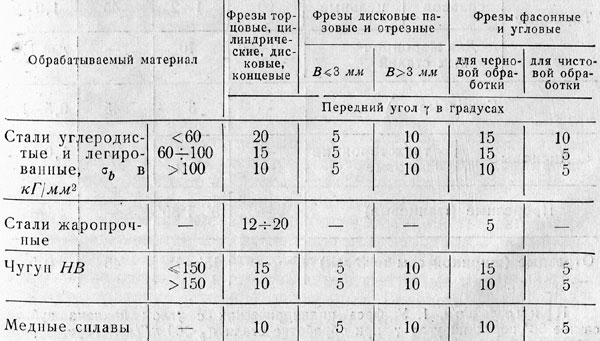
II. Задние углы
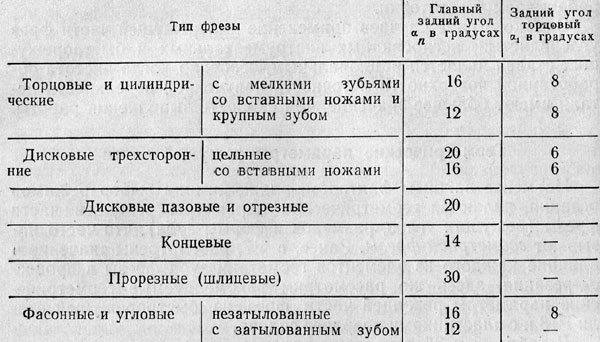
III. Углы в плане и переходной кромки

Примечания. 1. У фрез цилиндрических с углом наклона зубьев свыше 30° передний угол γ при обработке стали σ b меньше 60 кГ/мм
2 берется равным 15°.
2. У фасонных фрез с передним углом у больше 0° необходима коррекция контура при обработке точных профилей.
3. При обработке жаропрочных сталей торцовыми фрезами брать верхние значения передних углов, концевыми и цилиндрическими - нижние и средние.
4. На задней поверхности фрез при заточке оставлять круглошлифованную ленточку шириной не более 0,1 мм
. Зубья у фрез шлицевых (прорезных) и отрезных (круглых пил) затачиваются без оставления ленточки.
Внешний держатель и внутренний расточный стержень изготавливают круглые профили. Процессы обработки, которые используют держатели или расточные стержни, называются поворотными, и его основной характеристикой является то, что заготовки вращаются. Машина, используемая для поворота, называется токарным станком.
Инструмент на фотографии справа - это фрезерный инструмент. Режимы обработки, которые используют лицевые мельницы и концевые мельницы, называются фрезерными операциями, а его основной характеристикой является то, что инструменты вращаются. Машина, используемая для фрезерования, называется фрезерным станком.
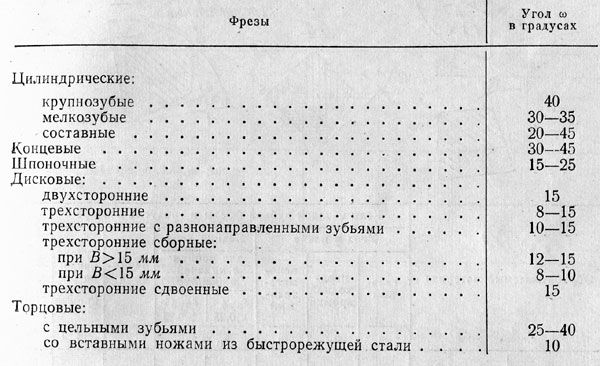
В табл. 37 - 40 приведены рекомендуемые значения передних и задних углов, главного, вспомогательного и переходного углов в плане, углов наклона режущей кромки и винтовых канавок, радиуса при вершине торцовых, цилиндрических, концевых и дисковых фрез с твердосплавными пластинами.
Фрезы, применяемые для обработки большинства заготовок, обычно поставляются инструментальными заводами с геометрическими параметрами, соответствующими ГОСТ, и фрезеровщику в отличие от токаря и строгальщика, почти невозможно изменять путем заточки режущие углы фрез. Вследствие этого приведенные в табл. 35 - 40 геометрические параметры режущей части фрез помогут фрезеровщику правильно выбрать соответствующую данной обработке фрезу из имеющихся в инсрументальной кладовой учебного и производственного цеха стандартных фрез. Однако основное назначение этих таблиц заключается в рекомендациях в том случае, если фрезеровщик захочет сам заказать инструментальному отделу стандартные или специальные фрезы с оптимальными для данной обработки геометрическими параметрами.
Ширина и глубина фрезерования
Фотография справа - это инструмент, который создает круглые отверстия в заготовках и называется сверлом. Индексируемые сверла вставки и паяные сверла производят относительно большие отверстия, а сплошные сверла создают меньшие отверстия. Основная характеристика бурения заключается в том, что его можно использовать как для фрезерных, так и для токарных станков.
Как упоминалось выше, режим резки состоит из трех основных стилей; токарная обработка, фрезерование и сверление. Выбирая подходящий режущий инструмент в соответствии с режимом резания, можно эффективно обрабатывать твердые металлы. Сегодня цементированные карбидные инструменты стали основным средством повышения производительности резки металла, в то время как исследования постоянно разрабатывают новые продукты для более точной и быстрой обработки для снижения производственных затрат.
Таблица 37
Геометрические параметры режущей части торцовых фрез с пластинками из твердого сплава
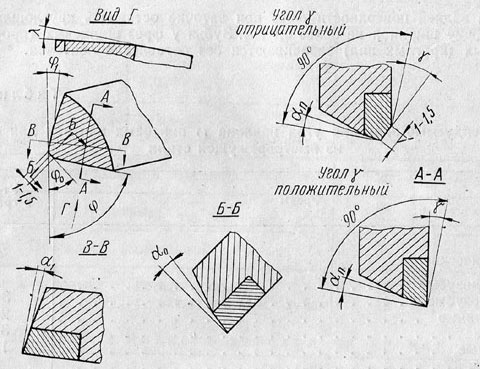
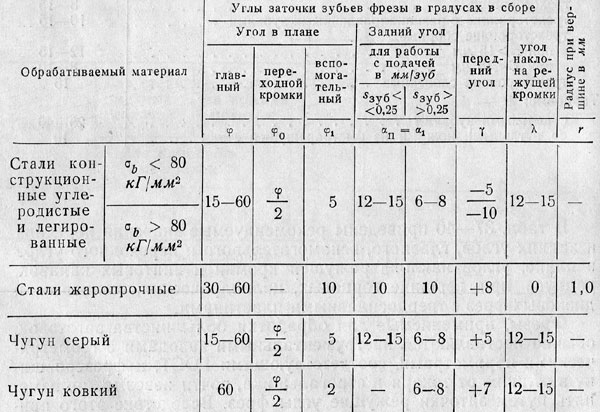
Примечание . Малые углы в плане φ = 15 - 30° следует применять, при обработке на жестких станках для черновых проходов с малыми глубинами резания или чистовых проходов с невысокими требованиями чистоты и точности к обработанной поверхности.
Предложена модальная модель фрезерных станков, подвергнутых временным периодическим нелинейным усилиям резания. Модель описывает явление бистабильности для определенных параметров резания. В технике эти области параметров называются небезопасными зонами, где стационарное фрезерование может переключиться на болтовню при определенных возмущениях. В математических терминах это области параметров, где периодическое решение соответствующего нелинейного дифференциально-временного уравнения с временной периодичностью линейно устойчиво, но его область притяжения ограничена из-за существования неустойчивого квазипериодического решения, выходящего из вторичного Бифуркация Хопфа.
Таблица 38
Геометрические параметры режущей части цилиндрических фрез с винтовыми пластинками из твердого сплава
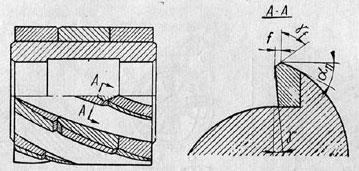

Примечание . На задней поверхности зуба вдоль режущей кромки допускается ленточка шириной не более 0,1 мм .
Представлен полу численный метод для определения границ этих бистабильных зон путем отслеживания движения краев фрезерного инструмента, поскольку они могут покидать поверхность заготовки во время операции резания. Это требует отслеживания неустойчивых квазипериодических решений и проверки их выпаса на периодически-периодическую поверхность переключения в бесконечномерном фазовом пространстве.
Ключевые слова: задержка, периодичность, фрезерование, тор, бистабильность, болтовня. Во многих аспектах механическая обработка металлов по-прежнему остается одной из важнейших технологий производства в наши дни. Его важность неоспорима в автомобильной, энергетической или воздушной промышленности. Обработка не только образует детали, но в большинстве случаев дает им окончательную форму, а это означает, что качество конечного продукта сильно определяется этими операциями резания.
Таблица 39
Геометрические параметры режущей части концевых фрез с пластинками из твердого сплава при обработке конструкционных углеродистых и легированных сталей
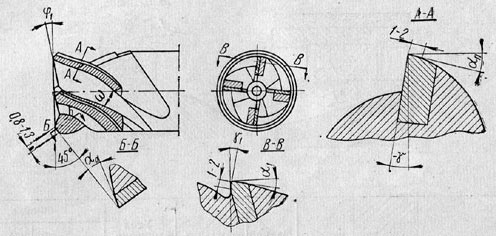
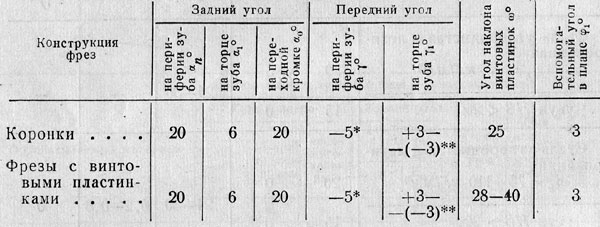
* При малой жесткости системы станок - приспособление - инструмент - деталь и при больших сечениях стружки (В
больше D
; t
больше 0,5D
), а также при работе с низкими скоростями резания при недостаточном числе оборотов шпинделя (v
меньше 100 м/мин
) передний угол γ назначается положительным + от 0 до +8°.
** Большие значения для мягких сталей, меньшие - для твердых сталей.
Ширина и глубина фрезерования
Ширина фрезерования
задается в чертеже детали. В случае обработки нескольких заготовок, закрепленных параллельно в одном зажимном приспособлении, ширина фрезерования равна ширине всех заготовок. В случае обработки наборами фрез ширина фрезерования равна суммарной ширине всех сопряженных поверхностей.
Глубина фрезерования
(глубина резания, толщина срезаемого слоя) дается как расстояние между обрабатываемой и обработанной поверхностями. В целях сокращения времени на обработку рекомендуется выполнять фрезерование в один проход. При повышенных требованиях к точности и чистоте обработанной поверхности фрезерование ведется в два перехода - черновой и чистовой. В отдельных случаях, при снятии больших припусков или при фрезеровании на станках с недостаточной мощностью, возможна обработка в два черновых прохода.
Таблица 40
Геометрические параметры режущей части дисковых фрез с пластинками из твердого сплава
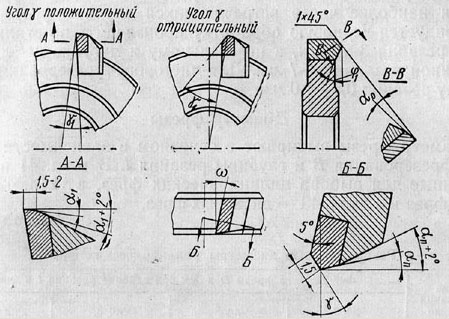
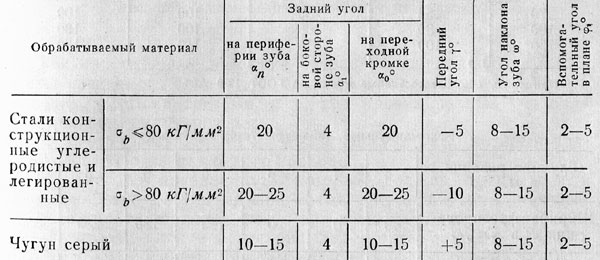
При фрезеровании стальных поковок, стальных и чугунных отливок, покрытых окалиной, литейной коркой или загрязненных формовочным песком, глубина фрезерования должна быть больше толщины загрязненного слоя, чтобы зубья фрезы не оставляли на обработанной поверхности черновин, так как скольжение по корке отрицательно действует на фрезу, ускоряя износ режущей кромки.
Для наиболее часто встречающихся случаев фрезерования рекомендуется черновую обработку производить по стали с глубиной резания 3-5 мм
, а по стальному и чугунному литью - с глубиной резания 5-7 мм
. Для чистового фрезерования берут глубину резания 0,5-1,0 мм
.
Диаметр фрезы
Диаметр фрезы выбирают в основном в зависимости от ширины фрезерования В и глубины резания t . В табл. 41 приведены данные для выбора цилиндрических фрез, в табл. 42 - торцовых фрез и в табл. 43 - дисковых фрез.
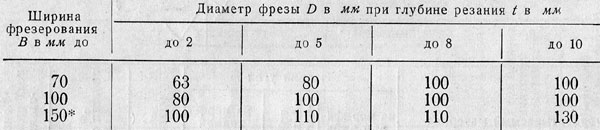
* Применять сборные составные фрезы по ГОСТ 1979-52.
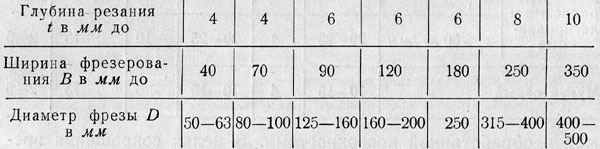
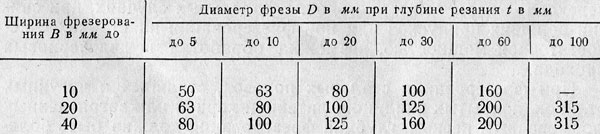
Рассмотрим влияние диаметра фрезы на производительность фрезерования.
Диаметр цилиндрической фрезы влияет на толщину среза
: чем больше диаметр фрезы D
тем тоньше получается срез; при одной и той же подаче s
зуб и глубине фрезерования t
.
На рис. 327 показан срез, получающийся при одинаковых глубине фрезерования t
и подаче s
зуб, но при разных диаметрах фрез. Срез, получающийся при большем диаметре фрезы (рис. 327, а), имеет меньшую толщину, чем срез при меньшем; диаметре фрезы (рис. 327, б).
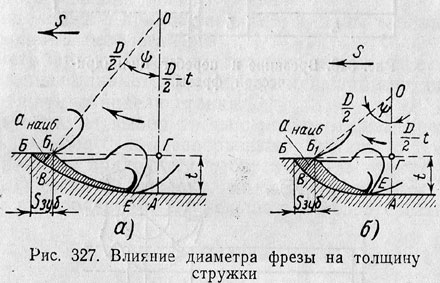
Так как удельное давление возрастает с уменьшением толщины срезаемого слоя а
наиб (см. табл. 38), выгоднее работать с более толстыми срезами, т. е. при прочих равных условиях при меньшем диаметре фрезы.
Диаметр фрезы влияет на величину пути
, который должна пройти фреза для одного прохода.
На рис. 328 показан путь, который должна пройти фреза при обработке детали длиной L
; на рис. 329 - путь, который должна пройти торцовая фреза при несимметричном фрезеровании заготовки длиной L
; на рис. 330 - путь, который должна пройти тортовая фреза при симметричном фрезеровании заготовки длиной L
.
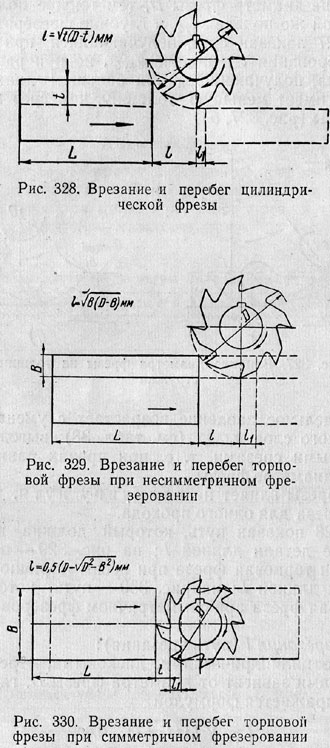
Величина врезания l
(путь врезания):
при работе цилиндрическими, дисковыми, отрезными и фасонными фрезами зависит от диаметра фрезы D
глубины фрезерования t
и выражается формулой
при работе торцовыми и концевыми фрезами при несимметричном фрезеровании зависит от диаметра фрезы D ширины фрезерования В и выражается формулой
при работе торцовыми фрезами при симметричном фрезеровании зависит от диаметра фрезы D ширины фрезерования В и выражается формулой
Величина перебега l
1 выбирается в зависимости от диаметра фрезы в пределах 2-5 мм
.
Следовательно, для уменьшения пути врезания и перебега фрезы, т. е. для сокращения холостого хода станка, целесообразно выбирать меньший диаметр фрезы.
В конце книги в приложениях 2 и 3, даны таблицы значений пути врезания и перебега фрез.
Диаметр фрезы влияет на величину крутящего момента
: чем меньше диаметр фрезы, тем меньший крутящий момент надо сообщить шпинделю станка.
Таким образом, выбор фрезы с меньшим диаметром является, казалось бы, более целесообразным. Однако с уменьшением диаметра фрезы приходится выбирать более тонкую, т. е. менее жесткую фрезерную оправку, поэтому приходится уменьшать нагрузку на оправку, т. е. уменьшать сечение срезаемого слоя.
Подача
Подача при черновой обработке
зависит от обрабатываемого материала, материала режущей части фрезы, мощности привода станка, жесткости системы станок - приспособление - инструмент - деталь, размеров обработки и углов заточки фрезы.
Подача при чистовой обработке
зависит от класса чистоты поверхности, обозначенной на чертеже детали.
Основной исходной величиной при выборе подачи для чернового фрезерования является подача s
зуб.
Для торцовых фрез на выбор подачи s
зуб оказывает способ установки фрезы относительно заготовки, что обусловливает величину угла встречи зуба фрезы с заготовкой и толщину срезаемой стружки при входе и выходе зуба фрезы из контакта с заготовкой. Установлено, что для торцовой твердосплавной фрезы наиболее благоприятные условия врезания зуба в заготовку достигаются при расположении фрезы относительно заготовки, как на рис. 324, в, т. е. при смещении фрезы относительно заготовки на величину С
= (0,03 - 0,05)D
. Такое смещение оси фрезы дает возможность увеличить подачу на зуб против подачи при симметричном фрезеровании (рис. 324, а) чугуна и стали в два раза и более.
В табл. 44 приводятся рекомендуемые подачи при черновом фрезеровании твердосплавными торцовыми фрезами для этих двух случаев.
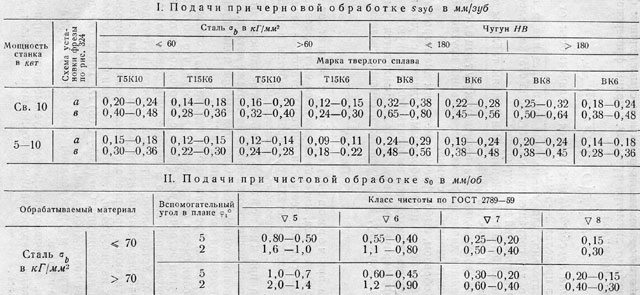
Примечания.
1. Приведенные значения черновых подач рассчитаны для работы стандартными фрезами. При работе нестандартными фрезами с увеличенным числом зубьев значения подач следует уменьшать на 15 - 25%.
2. В первоначальный период работы фрезы до износа, равного 0,2-0,3 мм
, чистота обработанной поверхности при чистовом фрезеровании снижается примерно на один класс.
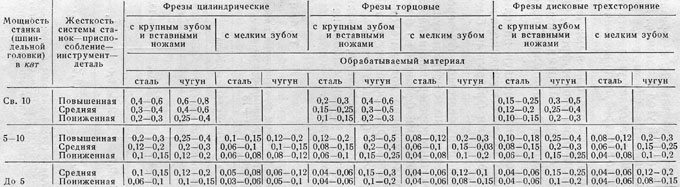
Примечание. Большие подачи брать для меньших глубины резания и ширины обработки, меньшие - для больших глубины и ширины обработки.

Примечание. Подачи даны для жесткой системы станок - приспособление - инструмент - деталь.
При торцовом фрезеровании твердосплавными фрезами на величину подачи влияет также главный угол в плане φ. Подачи, приведенные в табл. 44, рассчитаны на фрезы с φ = 60 - 45°. Уменьшение угла в плане φ до 30° позволяет увеличить подачу в 1,5 раза, а увеличение угла φ до 90° требует снижения подачи на 30%.
Подачи при чистовой обработке твердосплавными фрезами, приведенные в табл. 44, даются на один оборот фрезы, так как подачи на один зуб получаются слишком малыми. Подачи даются в зависимости от класса чистоты обработанной поверхности по ГОСТ 2789-59.
В табл. 45 приведены рекомендуемые подачи на один зуб фрезы при черновом фрезеровании плоскостей цилиндрическими, торцовыми и дисковыми трехсторонними фрезами из быстрорежущей стали Р18.
В табл. 46 приведены подачи при чистовом фрезеровании плоскостей цилиндрическими фрезами из быстрорежущей стали Р18, а в табл. 47 - при чистовом фрезеровании плоскостей торцовыми и дисковыми трехсторонними фрезами из быстрорежущей стали Р18. Ввиду малых значений подач на один зуб фрезы, получающихся при чистовом фрезеровании, в табл. 46 и 47 приводятся подачи на один оборот фрезы.
Следует иметь в виду, что работа с подачами, указанными в табл. 44-47, ставит непременным условием наличие минимального биения зубьев фрезы (см. табл. 50).
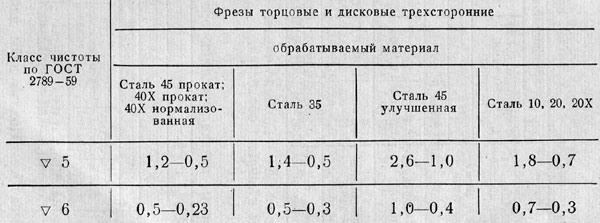
Примечание. Подачи даны для жесткой системы станок - приспособление- инструмент - деталь при обработке фрезами со вспомогательным углом в плане φ 1 = 2°; для фрез с φ 1 = 0 подачи можно увеличить на 50 - 80%.